Nissan will now be built faster and safer cars
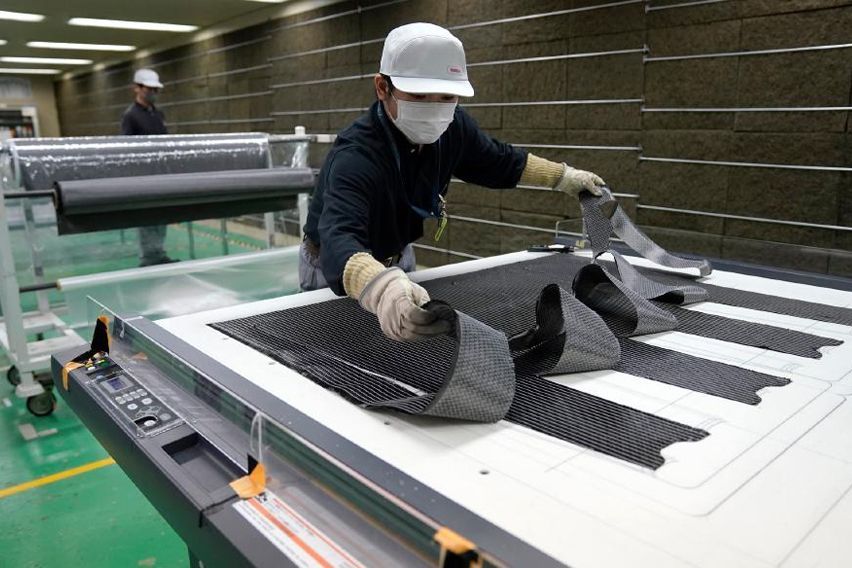
KUALA LUMPUR: Nissan has achieved a breakthrough in the production process of carbon fibre parts. We'll like to inform you that carbon fibre is the same material used in building sports cars, aircraft, and rockets. And now, thanks to Nissan, it'll find its way in more mass-market vehicles.
Nissan has been using carbon fibre parts in its vehicles for a while now; however, the entire process is a bit lengthy, leading to its limited use. However, Nissan engineers have found a new process of making carbon fibre reinforced plastics, CFRP, the material used to build car parts. We'll also like to inform you that compared to steel, the parts built from CFRP are expensive.
The CFRP is extremely strong and lightweight, and it makes the car safer and fuel-efficient. So, it is a win-win on all the fronts. When used to make upper body parts of the vehicle, it lowers the centre of gravity, making it more agile and exciting to drive.
The new process of developing CFRP reduces the lead time to build carbon fibre parts by almost half. Also, the cycling time of moulding comes down to 80 percent, compared to the conventional methods.
The current carbon fibre parts production method is called compression resin transfer moulding. And Nissan had introduced a new approach to this method. The earlier process involved moulding CFRP in the right shape by setting it in a die while leaving a slight gap between the upper die and the component. This gap was filled with resin, and the die is left to harden.
Under the latest development, Nissan's engineers can accurately simulate the resin's permeability while visualising resin flow behaviours in the die using a transparent mould and in-die temperature-sensor. Thus resulting in high-quality carbon fibre components in shorter intervals.
Also Read: Honda introduces PM2.5 cabin air filter
Sell your car at the best price


Nissan Car Models
Trending & Fresh Updates
- Latest
- Popular
You might also be interested in
- News
- Featured Stories
Nissan Featured Cars
- Latest
- Popular
Latest Nissan Car Videos on Zigwheels
